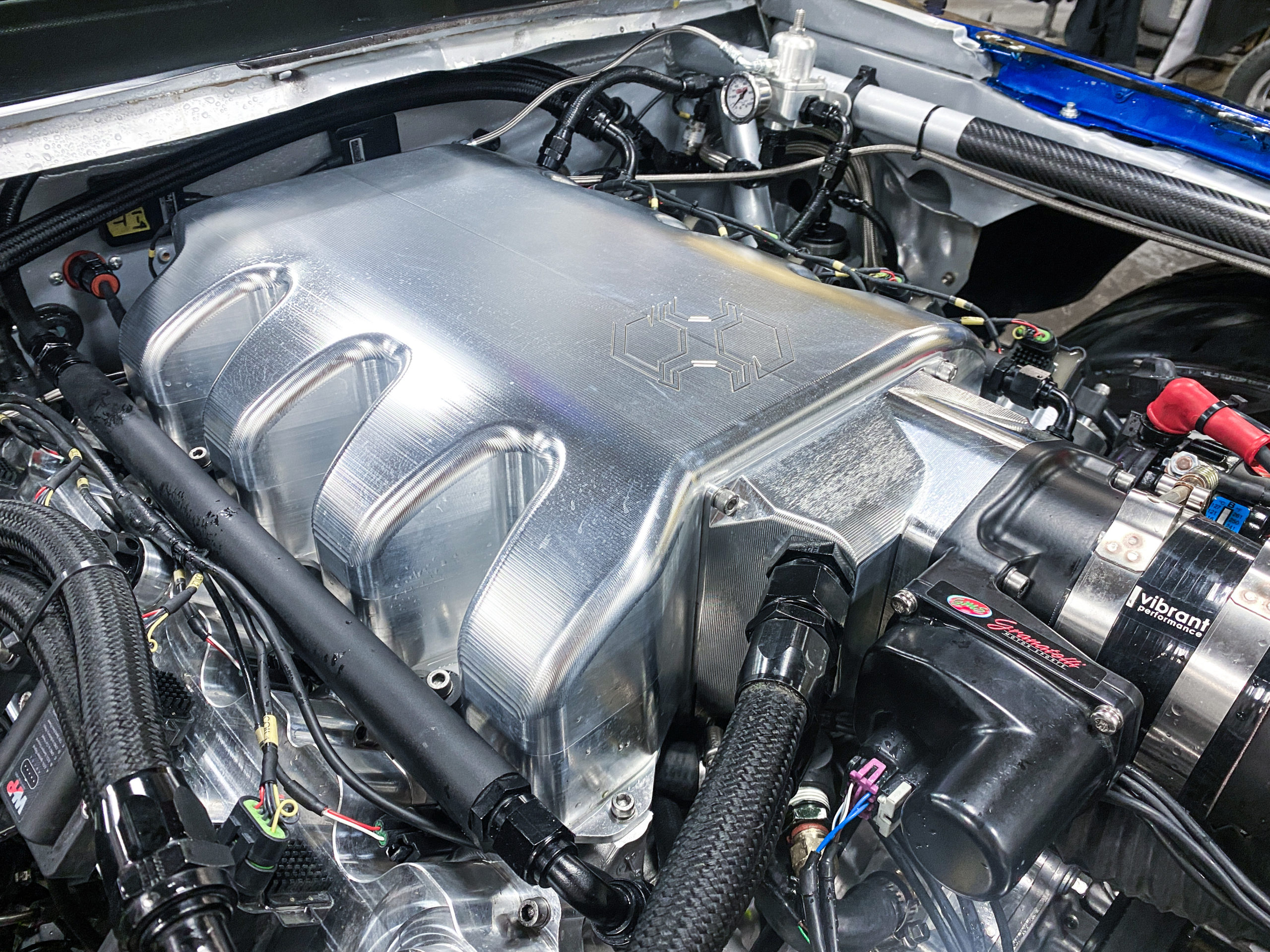
Low Profile
Intercooled
Billet Intake
Low Profile Intercooled
Billet Intake
Scroll down to learn more!
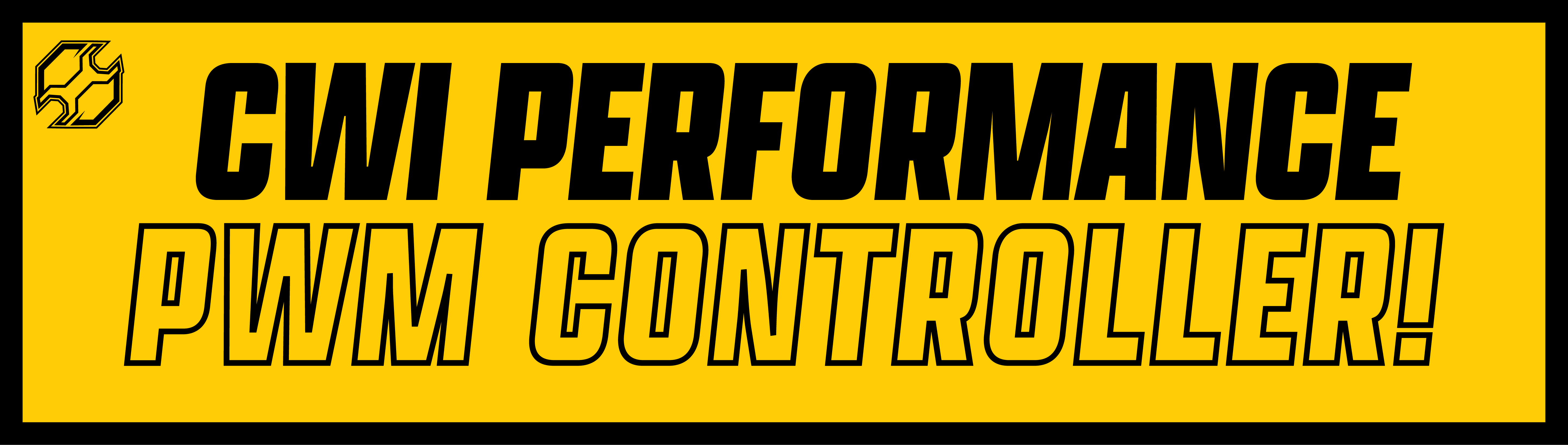
Brushed DC motors are some of the most commonly used electric motors, found in a wide range of applications from electronic cooling fans to electronic fuel pumps. These motors are simple and reliable, but their speed and torque can be difficult to control with traditional on/off switches. That’s where a Pulse Width Modulation (PWM Controller) comes in. By using a PWM controller with a brushed motor, you can achieve finer control over the motor’s speed and torque, resulting in a more efficient and effective system.
The PWM controller works by rapidly switching the voltage to the motor on and off at a fixed frequency. The duty cycle of the signal determines the amount of time the voltage is on versus off, which in turn controls the average voltage supplied to the motor. In contrast, a standard on/off switch simply connects and disconnects the motor from the power supply, resulting in a fixed voltage and limited control over the motor’s speed.
So, what are the benefits of using a PWM controller with a brushed motor? Let’s take a closer look.
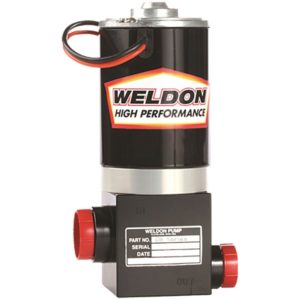
Why you should PWM an Electrical Fuel Pump
A fuel pump is an important component in the fuel delivery system of an engine. It is responsible for delivering the correct amount of fuel to the engine at the right time, ensuring that the engine runs smoothly and efficiently. However, a fuel pump that is always running at full power can be inefficient and can cause unnecessary wear and tear on the pump and other components of the fuel system.
This is where The CWI Performance PWM controller comes in. Our PWM controller can modulate the power supply to the fuel pump, allowing it to run at the appropriate speed for the current engine conditions. By adjusting the pulse width of the voltage signal, the PWM controller can effectively adjust the amount of power delivered to the fuel pump, allowing it to run at a lower or higher speed as needed.
You may be asking yourself, why would I want to modulate the fuel pump?
Well, here are some of the benefits of using a PWM controller to control a fuel pump:
Improved Fuel Efficiency:
OEM manufacturers today such as GM, Subaru, Nissan and others use PWM controllers to adjust their fuel flow for consistent and steady fuel pressure. By adjusting the speed of the fuel pump based on the engine’s needs, a PWM controller can help improve fuel efficiency. When the engine is running at low speed or at idle, the fuel pump can run at a lower speed, using less power and reducing fuel consumption.
Reduced Wear and Tear:
Running a fuel pump at full power all the time can cause unnecessary wear and tear on the pump and other components of the fuel system. By using a PWM controller to modulate the power supply, the fuel pump can run more smoothly and efficiently, reducing the risk of premature wear and tear.
Quieter Operation:
A fuel pump running at full power can be noisy, which can be bothersome to the driver and passengers. By using the PWM controller to adjust the speed of the fuel pump, the overall noise level of the fuel system can be reduced, resulting in a quieter and more comfortable driving experience.
Customizable Control:
With our Creative Werks Inc. PWM Controller, the speed of the fuel pump can be adjusted to meet the specific needs of the engine and driving conditions. This level of customization can help improve overall engine performance and efficiency, and can also help extend the life of the fuel system. These customizations can be made via an ECU with a PWM output, based on a 0-5V sensor or TPS Sensor.
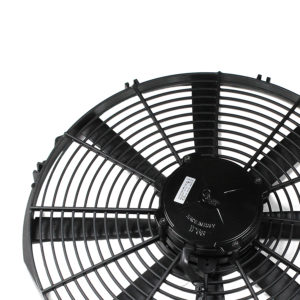
Why you should PWM an Electric Cooling Fan
Now there is a huge debate between brushed and brushless fans and whether or not your pro-touring car needs it. (note that the major difference between them is brushless fans have the capability to run variable speed but you pay a premium for those fans) in most street car // hotrod applications the need for brushless fans isn’t required, that’s where the brushed fans and the PWM controller come in.
With a PWM controller like ours at Creative Werks // CWI Performance, the controller allows you to control over fan speeds. This control allows you to be able to proactively cool the engine and under hood temps. In addition you can allow the motor to soft start and ramp up in speed, in comparison to hitting the fan with a a hard ON load. Dependent on the specific controller you choose you may be able to control multiple fans and have external override switches in place for A/C override or toggle switches.
So, what are the benefits of using a PWM controller with a brushed motor? Let’s take a closer look.
Greater control over speed and torque
One of the main advantages of using a PWM controller with a brushed motor is the ability to achieve greater control over the motor’s speed and torque. By adjusting the duty cycle of the PWM signal, you can precisely control the amount of power delivered to the motor. This can be especially useful in applications where precise speed control is necessary, such as preemptive cooling with fans, maintaining constant fuel pressure with multiple fuel pumps, and a skew of other applications.
Energy Efficiency
Another benefit of using a PWM controller with a brushed motor is energy efficiency. Because the PWM signal controls the average voltage delivered to the motor, you can reduce the voltage when less power is needed, resulting in less energy consumption. This can lead to significant energy savings over time in OEM applications, especially in applications where the motor runs for extended periods of time.
Reduced wear and tear
Using a PWM controller with a brushed motor can also help reduce wear and tear on the motor. When a motor is started with a standard on/off switch, it experiences a sudden surge of power that can cause excessive wear and tear on the motor’s components. By using our PWM controller the voltage is gradually ramped up, reducing stress on the motor and extending its lifespan.
Reduced heat generation
Finally, using a PWM controller with a brushed motor can help reduce heat generation. Because the voltage is switched on and off rapidly, the motor spends less time operating at full power, which can reduce heat generation and help keep the motor cool. This can be especially important in applications where the motor is located in a confined space or where heat buildup can be a safety hazard.
Perfect for Fan Controls
This controller can control a single or dual fan setup!
Free Configurator Software
Change the parameters of your PWM Controller with our FREE software.
Track Tested
Designed & tested on the track, perfect for everyday use!
The Details
- Dimensions: 7.25” x 3.75” x 1.75”
- Enclosure construction: 6061 Billet Aluminum, IP66 Rated
- Weight: 1.17lbs
- Protections: Reverse Polarity & Overcurrent Protection
- Max output: 200 Amp in-rush, 100Amp Continuous, Auxiliary Output .5 Amps
- Operating voltage: 12v
- Connectors: DT Series 12 Pin Deutsch (included), (4) 10MM Ring Terminal Studs
- PC communication: RS485-USB
- Download instructions here: PWM Controller instructions
- Download Configurator Here: PWM Configurator V212